Centrifugal Blowers
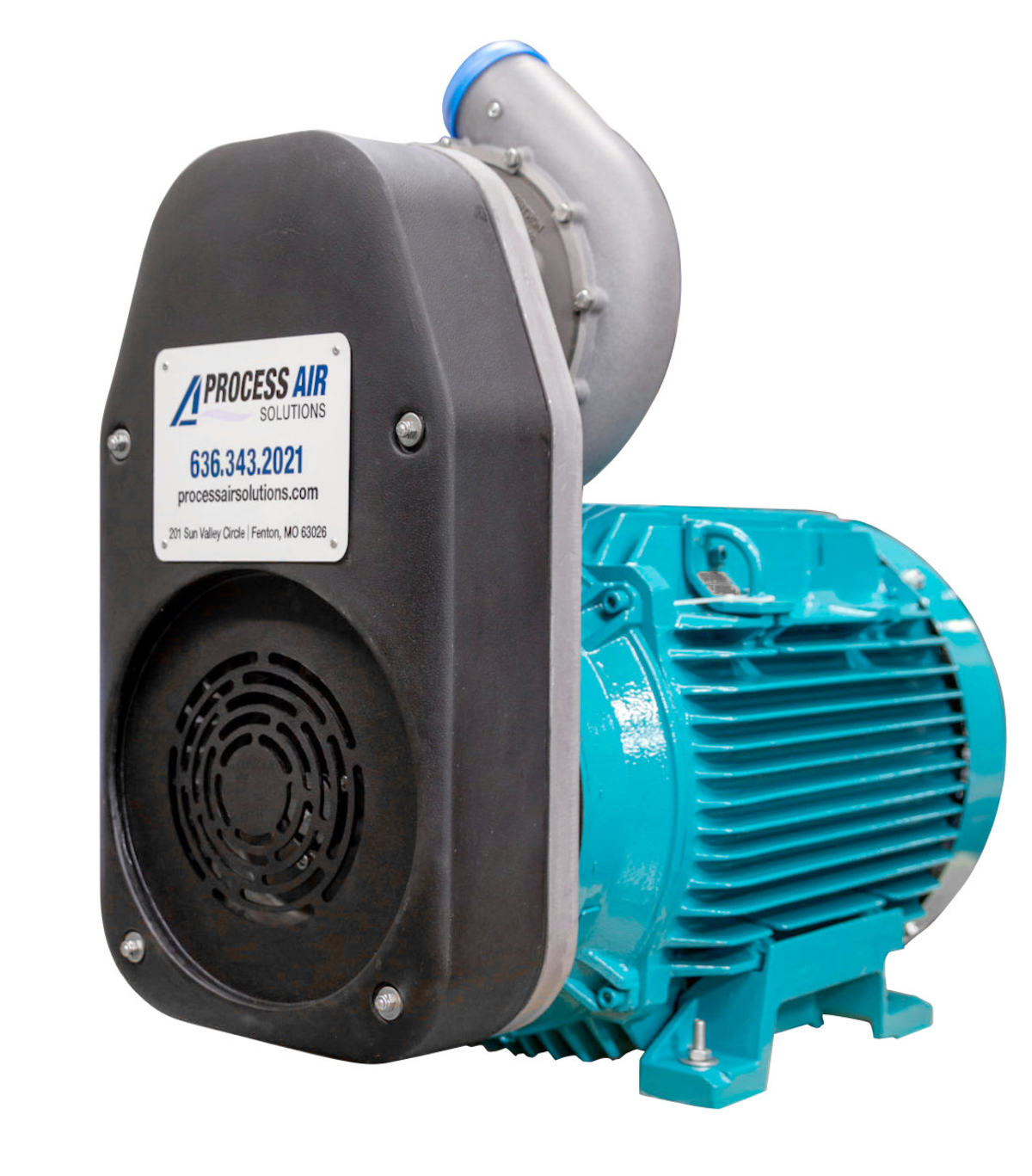
Volume: 200-1600 CFM
Pressure: 1-6 PSI / 30-150" H20
Vortron’s AirPower™ line of compact centrifugal blowers promises to raise the bar for industrial blower performance. Flow and pressure not attainable with competitive single stage products are now easily achieved. Three models are available: the flagship Z40e, the ultra efficient X40, and the scrappy J70. Each are specialists in their own right and are aerodynamically optimized for meeting specific flow and pressure requirements. All are clean-sheet designs developed from the ground up to deliver best performance, best durability, and best efficiency available anywhere today. With peak isentropic efficiencies reaching 80%, no other compact blower product even comes close.
Technology
A closer look reveals AirPower means business. All products are based upon modern centrifugal compressor design principles with aerodynamic performance vastly superior to common, but outdated technology. Manufacturing and quality are held to aerospace turbomachinery standards, enabling AirPower to consistently meet design performance and efficiency levels well beyond the competition. The elusive 100-in H2O at 1,000 SCFM is not only easily attained, it’s achieved at 80% efficiency!
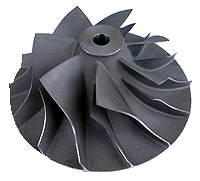
Development and Test
Based upon Vortech’s 12-plus years of industry-leading automotive supercharger design, development, and manufacturing, Vortron incorporates the same engineering and development excellence in the AirPower lineup. A fundamental difference that sets Vortron and AirPower apart is exhaustive testing. Years of analytical and empirical development were devoted to optimizing these designs, with numerous iterations tested and evaluated against stiff criteria. All accomplished with Vortron’s gas compressor test stand, developed and operated in accordance with SAE Standard J-1723 — a first and only in the industry! As such, Vortron is the only manufacturer which publishes compressor maps, derived from actual test data, for all AirPower products.
Inside AirPower
It’s immediately apparent; AirPower is different by design. Not only does the AirPower compact compressor outperform the competition, a variety of standard features are incorporated which clearly establish an exceptional product.
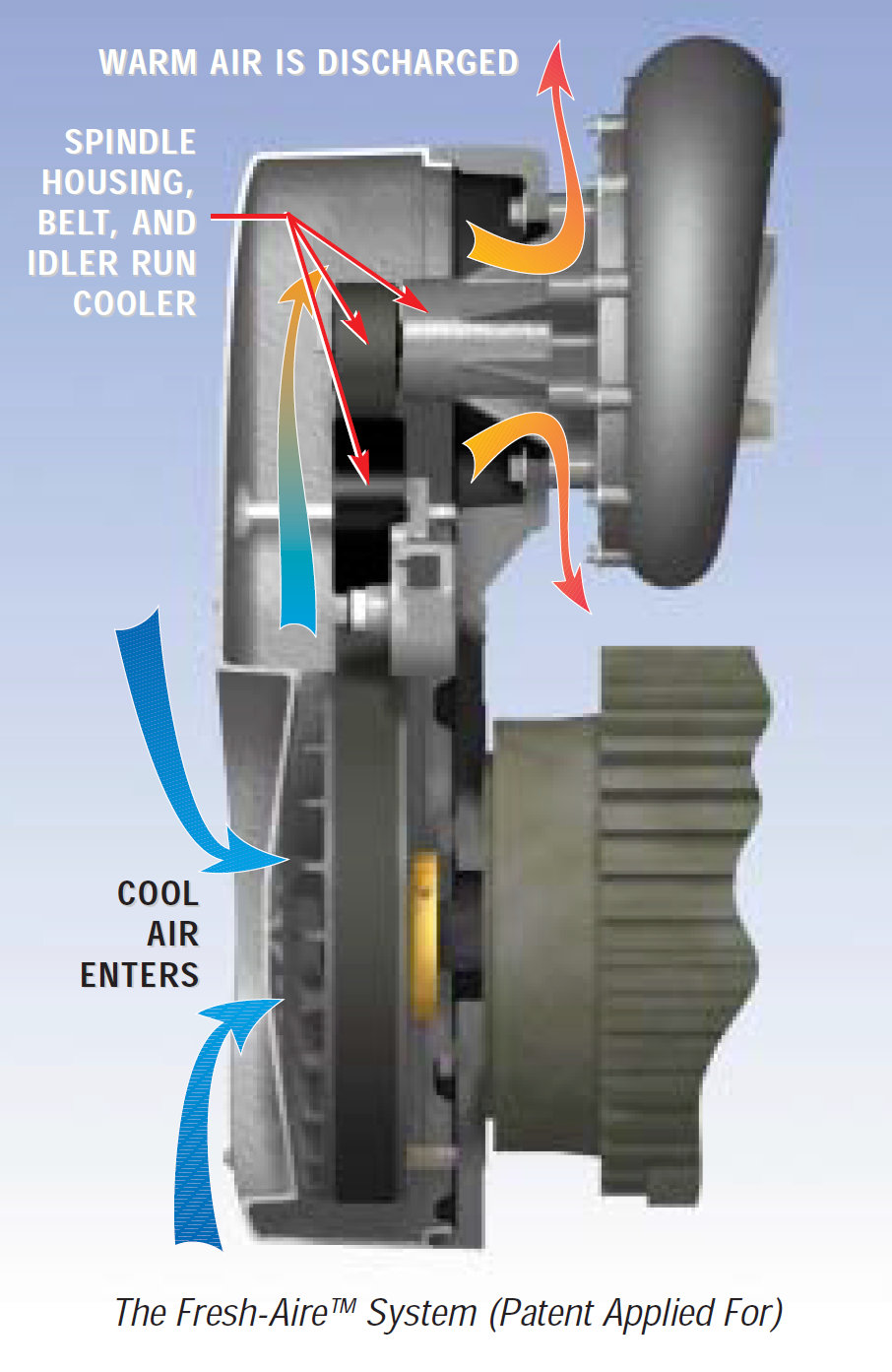
Spindle Assembly
Take note… AirPower spindles are entirely different from what you’re used to seeing. To begin with, the spindle housing is not exposed to the internal hot compressed air stream, common with competitive designs. Instead, AirPower incorporates it’s exclusive Fresh-Aire™ (patent pending) cooling feature, which supplies a completely separate, uncompressed cool air stream to the bearing housing. This limits temperature rise in the critical bearing and seal elements. Limiting temperature rise in the bearing system has a significant impact on longevity. In general, a 20° increase in running temperature will reduce grease life by a factor of one-half! AirPower's higher compressor efficiency limits temperature rise even more. The bearing system uses precision (ABEC 9) angular contact (A/C) bearings, with a duplex pair positioned outboard to support the belt load. A/C bearings are better suited for high-speed use and generate less friction, hence less heat and lower temperature rise than competitive deep groove ball bearing designs. The result: greater margin for speed and load capacity, meaning enhanced durability and extended life.
Tensioning and Belt Life
Automatic tensioning systems are now seen as standard, but AirPower incorporates a precision machined idler system with dual (proprietary) bearings for extended life. The entire drive system is fully enclosed and cooled by the Fresh-Aire system. Reasoning is simple: in general, an 18° temperature rise in the belt can also cut belt life in half! By carrying away heat, temperature rise in the belt and idler system is managed; again, reliability and life are maximized. Customers place a high priority on belt and idler performance – Vortron has engineered a solution!
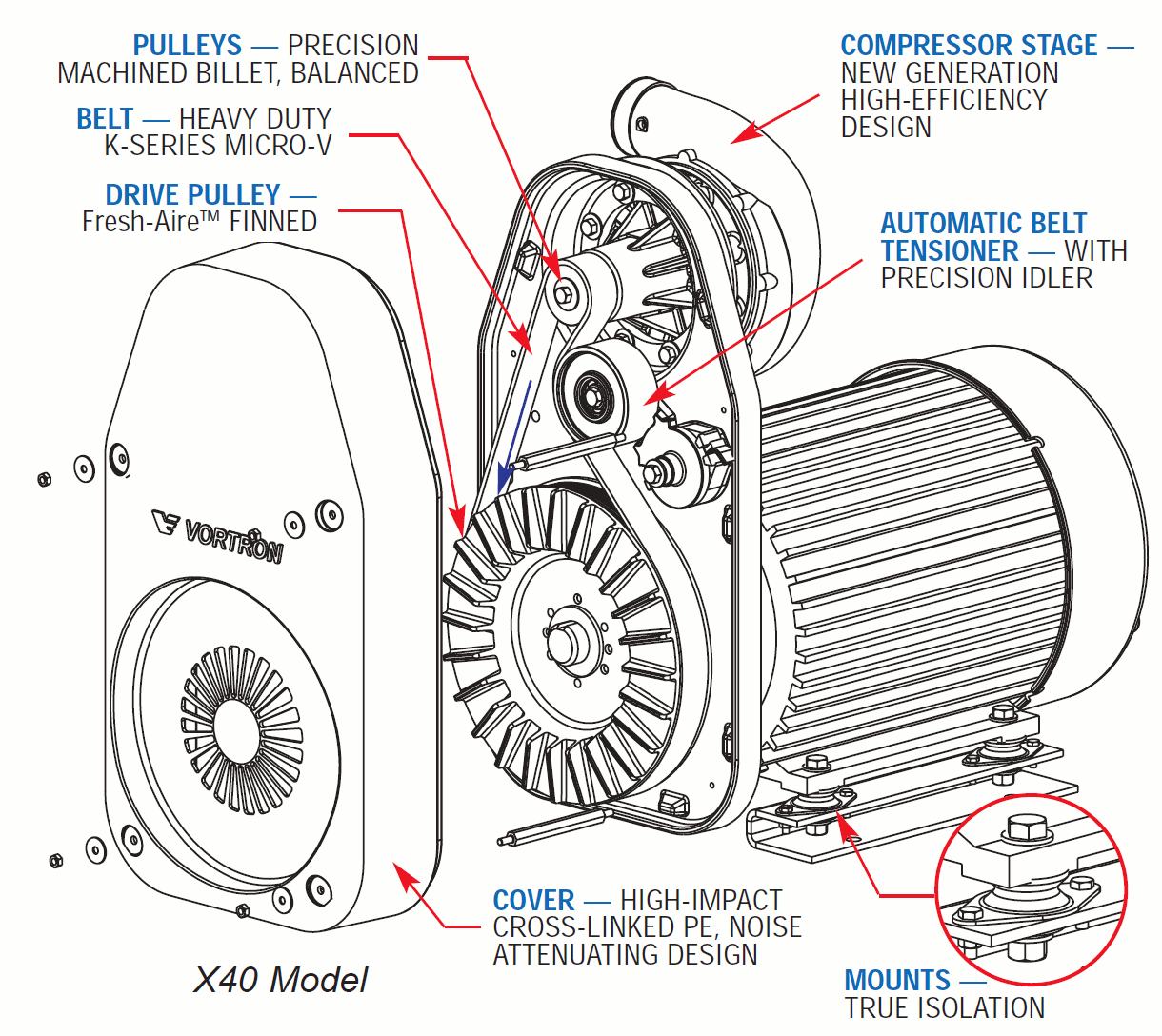
Precision Drive System Components
Designed and manufactured entirely by Vortron, our precision drive components add another level of quality and sophistication to the AirPower product line. Blower pulleys are machined from billet stainless steel and balanced to ISO G4 tolerances. Also part of the Fresh-Aire system, the unique drive pulley with integral cooling fins is cast aluminum, hard anodized, and balanced. This system makes sense as the large aluminum pulley offers additional capacity to conduct and carry away heat from the drive belt.
Cast Mounting Plate and Cover
Our customers continue to press for not only enhanced performance and greater reliability, but also quieter operation–a tough bill because making pressure quietly is not easy. But, Vortron ingenuity does it again. Another part of the Fresh-Aire system, the cast mounting plate and molded drive cover incorporate a sound-attenuating design to further manage potential noise sources.
Advanced Compressor Stage
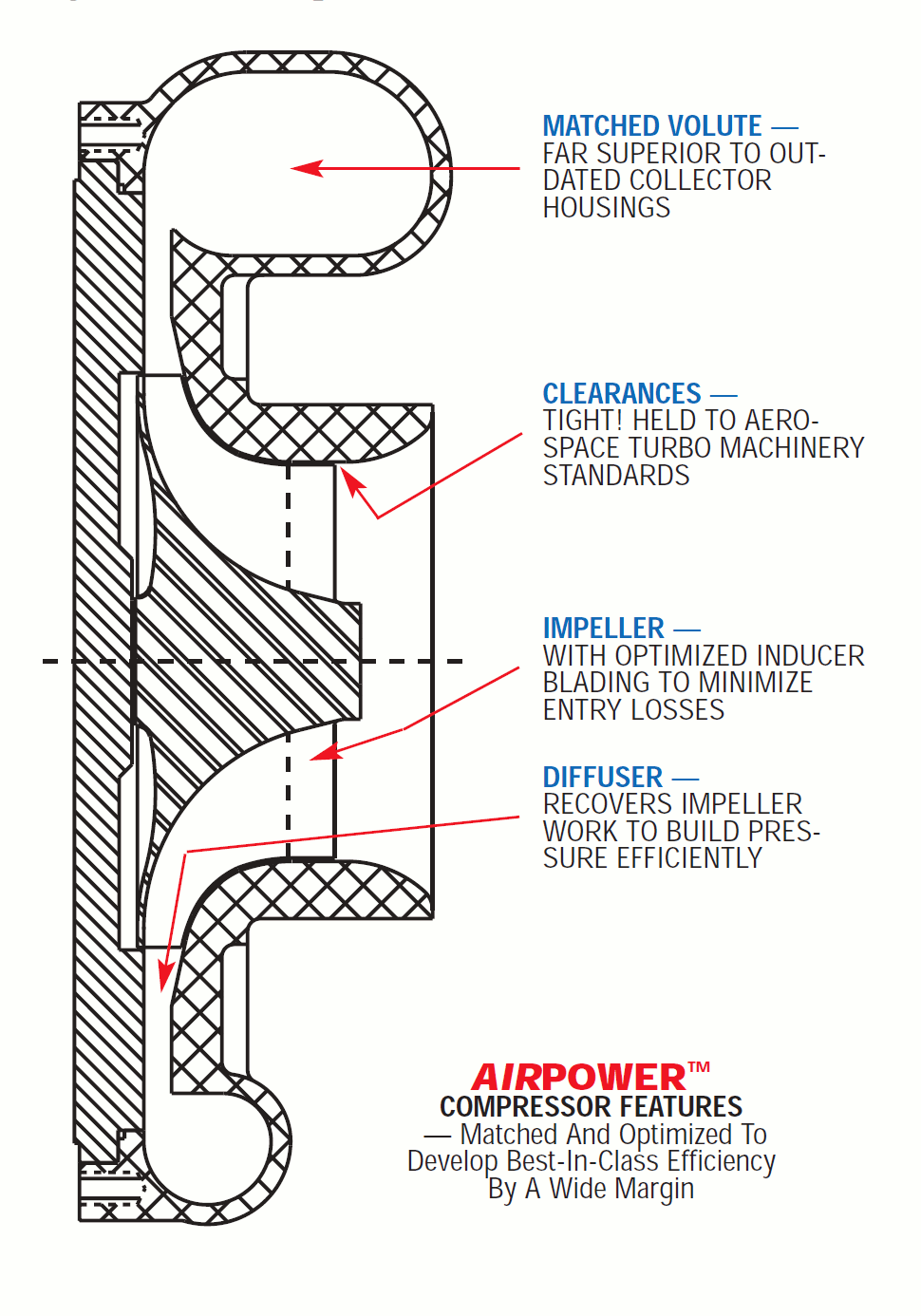
Here’s where the rubber meets the road! AirPower blower/compressor stages are highly evolved, thoroughly tested designs, originating from years of experience and thousands of production supercharger units. A simple visual examination clearly shows the difference. All AirPower compressors incorporate sophisticated impeller designs, coupled to either a channel or vaneless diffuser, with a progressive scroll, or volute exit stage. Impellers incorporate advanced aerodynamic features such as optimized inducer blading, splitters, and in some cases, exit rake and backsweep… all depending on the particular pressure/flow objectives. Rather than a simple change of blower speed to effect different "models" each AirPower differs aerodynamically so that best performance is attained for your specific application.
In order to effectively take advantage of impeller work, flow must be efficiently diffused so that pressure can be generated with minimal losses. Exclusive to AirPower , diffusers are incorporated, each optimally matched to the impeller flow physics, with many iterations tested and verified until maximum efficiency is achieved. Finally, a matched volute effectively collects and diffuses further, resulting in additional pressure rise.
The result? Isentropic efficiencies as high as 80%! In fact, all AirPower compressors achieve at least 75% peak efficiency, with better than 70% efficiency over a majority of design flow range (surge to choke). Note that these same efficiency levels are achieved at discharge pressures which clearly eclipse the competition, for a low-cost, single-stage machine. The AirPower Z40e, for example is capable of 170" H2O pressure at 1,200 SCFM, and 78% efficiency! Looking at it another way, a 20HP Z40e easily delivers the elusive 100" H2O at 1,000 SCFM.
It All Adds Up To…
More performance. Enhanced durability. Reduced energy consumption. Reduced annual operating costs. In other words, improved bottom line.